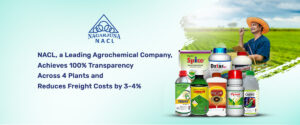
NACL, a Leading Agrochemical Company, Achieves 100% Transparency Across 4 Plants and Reduces Freight Costs by 3-4%
Case Study NACL, a Leading Agrochemical Company, Achieves 100% Transparency Across 4 Plants and Reduces
Case Study NACL, a Leading Agrochemical Company, Achieves 100% Transparency Across 4 Plants and Reduces
Table of Content: Imagine this—you’ve finalized a critical shipment of transformers and switchgear for an upcoming project, but
Logistics is the backbone of the Metal Industry. It relies significantly on seamless SCM to ensure efficient inbound & outbound movements of raw materials and finished goods.
This blog contains excerpts from our recent webinar on turning 5 critical logistics challenges in the metal industry into opportunities delivered by industry experts: Mr. Anshuman Datta, principal partner at Schlau Consulting and Solution Private Limited; Mr. Satyendra Singh, General Manager, Supply Chain and Logistics at Jaideep Ispat and Alloys Pvt Ltd and Shivani Rathogi, Consultant – Metal Industry at SuperProcure.
Digital TMS solutions can unlock a plethora of opportunities to turn existing roadblocks into opportunities. They harness the power of scalability, tracking, collaboration, and transparency across the logistics workflow to help logistics experts identify grassroots challenges and plan viable mitigation strategies.
Manual vehicle procurement leads to delays due to several factors:
The procurement and indenting processes involve extensive information sharing and acquiring updates on freight finalization status, rates, and location. Lack of centralized communication results in chaos, discrepancies, and inefficient vehicle placement.
Waiting for indent acceptance and checking its compliance with contracts involves extensive documentation, follow-ups, vehicle-load matching, and data sharing, which can lead to delayed vehicle placement.
Transporters often fail to place the vehicle at the contracted rates; thus, shippers usually lose significant time & money looking for another transporter willing to comply with the contract rates and terms. Time-intensive reallocation process increases the vehicle placement time.
Digitalization enables better communication and unlocks transparency, preventing inefficient vehicle placement.
In the metal industry, the freight costs vary according to PMT or PKPT (i.e., weight or both, weight & distance) instead of number of vehicles/boxes, etc. So, if the weight and/or distance increases, the cost will increase.
The metal industry deals in bulky orders, requiring much storage space, and specialized vehicles for distinct product categories. Adhoc procurement for bulk movements results in high freight costs for metal businesses.
Manually reaching out to the pool of vendor partners, inquiring about individual rates, researching current industry benchmark rates, and frequently negotiating over multiple communication channels is a complex and time-consuming process. It is an ineffective way to deal in a dynamic market that is subject to regular fluctuations, thereby affecting the timely availability of vehicles and improving cost savings.
Due to the time constraint and lack of historical data visibility, the right freight rate discovery can be time-consuming, leading to dispatch delays. Manually comparing and evaluating the costs with current spending increases the chances of errors and costs.
Lack of data visibility on routes hinders route planning and optimization. This can often result in longer routes prone to congestion and traffic, increasing fuel consumption, freight costs, and penalty clauses.
Digitalization helps shippers optimize freight costs, improve visibility, and unlock the following advantages:
The industry deals with bulk orders and normally observes 100-150 trucks each day for loading and unloading- this also causes plant traffic. The in-plant movements are often delayed due to extensive traffic, the loading point, and the manual inspection certificate process.
Inspection is a critical in-plant process that happens at the gate. This results in gate-in delays and traffic outside the plant. Thus, gate-in is the first point that is prone to significant delays.
Lack of transparency on gate-in/gate-out operations hinders the workflow. Multiple stakeholders lack accurate updates on vehicle status when it reaches the plant, affecting loading, dispatches, and vehicle TAT.
With manual processes, the information regarding dock management remains scattered, resulting in hidden bottlenecks. Coordinating with the loading team, the drivers, and other personnel becomes cumbersome and time-consuming, resulting in delays and inefficient in-plant management.
As pointed out by one of our speakers, Shivani Rastogi, consultant metal industry at SuperProcure, “Manual in-plant management lacks stage-wise monitoring. It involves extensive paper-based checkpoints, error-prone inspections, and inefficient coordination, leading to loading detention.”
Digitalization can prevent critical intricacies within the plant with the following:
Transparency and collaboration are critical to the metal supply chain.
Effective collaboration among stakeholders is imperative as multiple movements are managed through the supply chain—inbound, outbound (primary, secondary, last-mile), and inter-unit transfers. However, working with siloed and legacy systems lacks holistic communication and data exchange, especially with external stakeholders, which often leads to delays and discrepancies. Often, external vendors and partners lack visibility due to limited or no access, leading to increased manual coordination and dissatisfaction.
Without transparent and real-time access to data, managers cannot make informed decisions regarding vendor selection, inventory levels, or transportation routes. This affects decision-making, leading to increased costs and decreased efficiency. Transparency is crucial for identifying and mitigating risks such as disruptions in transportation, optimum freight rates, supplier reliability issues, or quality control. Transparency is crucial for ensuring compliance and accountability. It is difficult to track and trace products, verify supplier compliance, or maintain audit trails. Lack of transparency also impacts customer satisfaction, as it may lead to delays in order fulfilment, inaccurate delivery estimates, or difficulty in tracking shipments.
Digitalization provides a common platform for centralizing the entire process, ensuring improved transparency and collaboration.
In ex-works/ex-factory, transportation and transit risk scope fall on the buyer or the customer. The customer arranges for the pickup and transportation of goods and hence, has to coordinate with transporters. Often, the customer cannot do this independently. So, they rely on a mediator or an agent/broker, to help them source vehicles. Ex-factory dispatches are prone to several gaps.
For ex-factory dispatches, the selection of a supplier often hinges upon several key factors, including proximity to the buyer’s location and the logistical considerations associated with transportation. When arranging for the transport of goods, either independently or through an intermediary such as an agent or broker, buyers frequently prioritize suppliers situated closest to their operational base. Additionally, considerations such as the availability of transporters, optimal routes, and associated costs play pivotal roles in decision-making. When buyers opt for a supplier based on geographic proximity or logistical convenience, there exists the risk of purchasing products offered by competitors, leading to a loss of sales.
Due to a lack of control over vehicle placement, supply chain managers are subjected to delays at every tier. Delayed and inefficient placement affects subsequent stages, inventory management, and customer satisfaction.
Ex-factory dispatches need data updates at every step for strategic management. Other stakeholders, like the gate security and sales teams, cannot view the status of the orders, hampering communications and leading to inefficiencies. At the gate, vehicle checking is a time-intensive task due to the need for more information on the number and type of vehicles.
Digital TMS solutions can give prior intimation of vehicles arranged by customers with the following:
In conclusion, the metal industry faces a myriad of logistics challenges, ranging from inefficient vehicle placement to a lack of transparency and collaboration across the supply chain. However, digitalization presents a transformative solution to these challenges. By leveraging digital TMS solutions, organizations can unlock a host of opportunities to streamline operations, optimize costs, and enhance overall efficiency. From improving communication and transparency to enabling real-time visibility and collaboration, digitalization offers a comprehensive toolkit for turning existing roadblocks into opportunities for growth and success. Embracing digitalization in logistics holds the key to overcoming industry challenges, and propelling the metal industry into a future of innovation, resilience, and competitive advantage.
Subscribe to our blog for the latest news and updates
Ensure your company’s data is completely secure and compliant with the latest regulatory standards
5/5
4.5/5
5/5
4.5/5
Solutions
Industry
Real Time Freight Sourcing And Collaboration Platform
Unit 3B, 4 Bakul Bagan Row, Lansdowne Market. Kolkata- 700025, India
Share us the details to connect to a relevant team member.