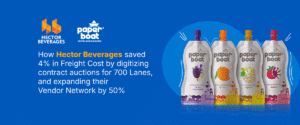
How Hector Beverages saved 4% in freight costs by digitizing contract auctions for 700 lanes, and expanding their vendor network by 50%.
Case Study How Hector Beverages saved 4% in freight costs by digitizing contract auctions for
Case Study How Hector Beverages saved 4% in freight costs by digitizing contract auctions for
Table of Content: Choosing the right Transport Management System (TMS) can be overwhelming. With every vendor claiming to
In-plant logistics plays a vital role in ensuring smooth operations within manufacturing facilities, where the flow of materials and products must be consistently reliable. However, traditional management methods often fall short, with issues like limited visibility, operational inefficiencies, and execution delays disrupting the process.
Today, that landscape is changing. Automation is stepping in as the key driver of this transformation, offering a more efficient, cost-effective approach to managing in-plant logistics. The benefits are clear: from more precise material handling to reducing costs and enhancing scalability, automation has the power to reshape how logistics leaders manage their facilities.
In this blog, we’ll dive into how automation is revolutionizing in-plant logistics, giving you the insights needed to stay ahead in a competitive market.
In-plant logistics refers to managing and optimizing the flow of materials and information across stages like- receiving raw materials, storage, inventory management, internal transportation, and the delivery of finished products.
Inspection:
Materials and components are examined to check quality and quantity compliances.
Weighment:
Materials are weighed to verify the volume as per shipping documents.
Documentation:
Detailed records are updated to reflect the accuracy of items received.
Warehousing:
Materials are stored and organized in designated areas for easy access.
Inventory Management:
Inventory levels are monitored and managed consistently to ensure on-time availability.
Layout Planning:
Designing a layout plan in consideration of inventory profile, order patterns and convenience goals.
Pick up and Drop:
Picking and dropping goods from their designated locations until the final production stages.
Tracking:
Partially finished products are tracked as they move through different production stages.
Optimization:
The flow of WIP is optimized to minimize bottlenecks and reduce lead times.
Weighment:
Finished products are weighed to ensure they meet order specifications.
Storage:
Products are moved to storage areas, ready for shipment or further processing.
Packaging:
Finished products are packaged according to shipping requirements.
Documentation:
Shipping documents are prepared and updated.
Data Integration:
Real-time data on inventory levels, production status, and material movements are integrated into ERP or WMS systems for seamless monitoring and utilization.
Reporting:
Regular reports are generated for decision-making and compliance tracking.
Schedule a demo to improve your in-plant logistics efficiency at every step Book a Demo
As customer expectations continue to rise, the pressure for agile planning and real-time responsiveness becomes more intense. Achieving this level of efficiency requires precise control over in-plant logistics. In fact, 83% of companies surveyed recognize the importance of specialized logistics systems for improving internal transport performance.
Effective in-plant management is crucial for preventing material shortages, minimizing production delays, and optimizing resource allocation. By streamlining processes and ensuring accurate material handling, it mitigates errors and associated risks.
Efficient in-plant operations rely on accurate demand forecasting to balance workload and prevent resource waste. Proactive equipment maintenance further minimizes errors and downtime.
Strategic in-plant logistics optimizes productivity by eliminating rework, streamlining material flow, minimizing waste, and accelerating output.
Inefficiencies within the in-plant workflow can lead to significant production delays, increased costs, and decreased overall productivity. Here are some of the most pressing challenges:
Inefficient material flow, space constraints, and labor shortages hinder operations. Typically, manual processes and outdated technology contribute to errors and delays. Additionally, balancing production requirements with logistics capabilities is a constant challenge.
Unforeseen hurdles like equipment breakdowns, material shortages, quality non-compliance, and labor constraints can lead to production delays and bottlenecks. Also, inefficient customer demand planning can further complicate scheduling.
Process and transportational delays within the plant due to lack of movement visibility, complexities of product lines, inadequate space utilization and improper use of handling equipment result in accelerated operational costs.
Privitive in-plant modules with data silos, lack of real-time visibility, dynamic demand fluctuations, limited resources, and complex operational constraints often hinder decision-making efficiencies.
Automation is emerging as a game-changer, offering the potential to revolutionize operational performance and giving businesses the agility they need to stay competitive
SP integrated logistics management systems (ILMS), which integrate with enterprise resource planning (ERP) and warehouse management systems (WMS), providing a centralized platform for managing in-plant operations. The impact of automation can be traced across the following core process stages:
To understand how multi-enterprise collaboration can help improve logistics efficiency, as an example, let us explore a few use cases with one of the key stakeholders – carriers/transportation partners, that a TMS solution can assist with to overcome some of the challenges highlighted previously.
Advanced technologies like real-time tracking, IoT sensors and data analytics offer unparalleled visibility into operations, identifying bottlenecks and optimizing resource use. Automation of routine tasks frees up staff for strategic thinking, while digital tools enhance communication and accuracy.
Fostering a collaborative workflow and tools facilitate knowledge sharing, problem-solving, and process improvement. Informed predictions and planning around demand enable strategic inventory management and optimization. Actionable plans on resource utilization, route optimization, data integration and production schedule plans empower in-plant efficiencies.
Optimize the shipping process with detailed arrival and departure plans and Coordinate vehicle schedules to prevent delays and inefficiencies and keep things moving smoothly. Actionable plans on resource utilization, route optimization, data integration and production schedule plans empower in-plant efficiencies.
Enhance communication and data interchanges across cross-functional departments—production, warehouse, shipping, and others. This prevents gaps, confusion, and handling errors and strengthens planning and risk management.
The evolution of in-plant logistics, driven by automation and digital innovations, reshapes operations and sets new benchmarks for organizational success. Companies that adopt these advancements can achieve substantial cost savings, improved productivity, and streamlined workflows, establishing themselves as leaders in their respective industries.
As organizations shift towards more agile and transparent planning, now is the perfect moment to act. Unlock the true potential of your in-plant logistics with SP ILMS solutions and drive your organization towards a future of efficiency and excellence.
Take the first step towards supply chain transformation today! Book a Demo
Subscribe to our blog for the latest news and updates
Ensure your company’s data is completely secure and compliant with the latest regulatory standards
5/5
4.5/5
5/5
4.5/5
Solutions
Industry
Real Time Freight Sourcing And Collaboration Platform
Unit 3B, 4 Bakul Bagan Row, Lansdowne Market. Kolkata- 700025, India
Share us the details to connect to a relevant team member.